Continuous Polyurethane (PU) Sandwich Panel Production Line
Polyurethane Sandwich Panel Production Line
1. Product description
Polyurethane Sandwich Panel Line is the automation equipment that can continuously and efficiently produce polyurethane sandwich panels of exquisite and diverse shapes. This Sandwich panel line has the advantages such as high durability, easy management, technology equivalent to those of advanced European companies and relatively competitive price, and it is the excellent facility that has been exported to Europe, Asia, Middle East, Russia and so forth as well as domestic market and is well received from customers.
Polyurethane Sandwich Panel Line consists of Un-coiler that inputs and releases coil, Roll Forming Unit that makes shape of coil, PU Forming Unit that sprays PU solution, Laminating Unit that makes the shape of sandwich panel, Panel Cutting Unit that cuts the fabricated sandwich panel, Cooling Conveyor Unit that finishes products hardening the cut panel sufficiently at intervals, Auto Stacking Unit that loads the finished panels, and Panel Packing Unit that packs the loaded panels with plastic wrap and discharge them.
2.Main equipment
1) Un-Coiler
Un-coiler is a device that inputs steel coil to the upper and lower parts of sandwich panel to feed it stably.
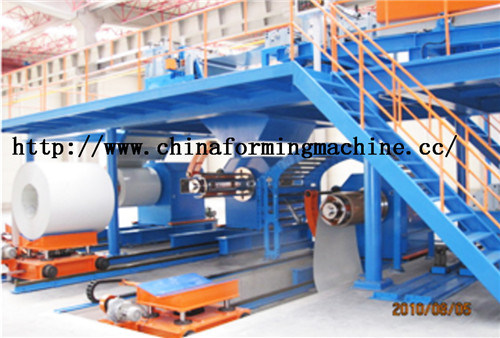
Â
2) Roll forming machine
It is a device that continuously gives shape to sandwich panel as steel coil fed from Un-coiler is engaged between the upper and lower sections of a metal roller.
Â
3) PU foaming mahcine
It consists of the nozzle and pump that spray polyurethane solution, a tank that stores solution, various catalysts and gas, and a traverse that enables to spray PU solution evenly, and the device is designed considering high precision and the reliability of maintenance. A convenient control panel is equipped with for users' easy control of various data required for foaming process.
Â
4)Â Laminating unit
It is a device that makes the shape of sandwich panel applying constant pressure and heat to the upper and lower steel plate foamed with polyurethane.
It designed in perfect structure that has a stiffness and durability and as well as the side blocks to enable the rapid of product replacement.
Â
5)Â Panel cutting unit
A device that cuts sandwich panel fabricated at Laminating Unit to the length desired by users using a band saw.
Different types cutting such as wheel cutting and band saw cutting has developed to correspond for the customer's needs.
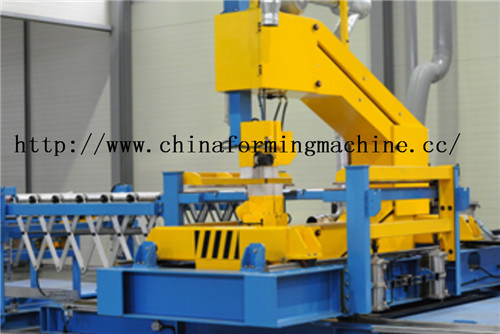
Â
6) Cooling conveyor unit
In case that a certain time is required till completely hardening since polyurethane sandwich panel is thick, Cooling Conveyer enables to allow sufficient hardening time prior to stacking and packing panels.
7) Â Auto stacking unit
As is a device that automatically stacks the finished panels, the quantity desired by users can be loaded continuously by loading pattern of vacuum suction plates or lift conveyor And in case of roofing material, cross stacking is available, if necessary.
Â
8)Â Panel packing unit
A device that packs panels loaded at Auto Stacking Unit with plastic wrap on 4 sides or 6 sides and discharges them.
Applying pallet systems to insert the EPS block automatically and it makes handy for cargo transportation and storage the panels.
3. Specification of Sandwich Panel Line
Â
1. Producing speed | Min. 2meter/min ~Max. 15meter/min |
2. Length of Double belt conveyor | 20~40meter |
3. Factory Electricity | 380V x 50Hz x 3Ph (User's choice available) |
4. Controlling Electricity | A.C. 220V (User's Choice Available) |
5. Factory's Area | 130~150(Length) x 30m(Width) x 6m(Height) |
6. Pressure of compressed air | Over 6 bar required |
7. Production | 4~5 person |
4.The general specification of PU panel produced
 1. Panel length | Min. 2,000mm in auto mode |
Max. 18,000mm (±3mm) | |
2. Effective width | 1000mm for roof |
600mm~1200mm for normal wall | |
3. Panel thickness | Available thickness from 30~200mm |
(depended upon heights of the side sealing block.) | |
4. Top and Bottom layer | Pre-painted Galvanized coil |
For ASTM A 526-85, JIS G 3302 SGCC | |
Thickness = 0.4mm ~ 0.7mm | |
5. insulation | PUR hardened and PIR / Pentane |
6. Density of Insulation | 30kg/m3 ~ 50kg/m3 |
5.Warranty
one year warranty from date of shipment, and we will provide the technical support for the whole life.
Â
Welding Neck Flanges are easy to recognize at the long tapered hub, that goes gradually over to the wall thickness from a pipe or fitting.
The long tapered hub provides an important reinforcement for use in several applications involving high pressure, sub-zero and / or elevated temperatures. The smooth transition from flange thickness to pipe or fitting wall thickness effected by the taper is extremely beneficial, under conditions of repeated bending, caused by line expansion or other variable forces.
These flanges are bored to match the inside diameter of the mating pipe or fitting so there will be no restriction of product flow. This prevents turbulence at the joint and reduces erosion. They also provide excellent stress distribution through the tapered hub and are easily radiographed for flaw detection.
This flange type will be welded to a pipe or fitting with a single full penetration, V weld (Buttweld).
Steel Pipe Welding Neck Flange,Rigid Butt Welding Flange,Welding Neck Flange For Pipe,Carbon Steel Flange Customization
Fuyuan Marine Accessories Co., Ltd , https://www.fuyuanmarineparts.com