Customer Testimonial: Shape Corp. Adopts Moldex3D to Make Simulation into Reality
Â
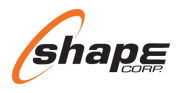
- Customer: Shape Corp.
- Industry: Automotive
- Solution: Moldex3D eDesign
- Country: India & USA
The following testimonial was received from Mr. Tyler Forbes, the global plastics technical manager at Shape Corp., sharing his team’s experience with Moldex3D.
Why Choose Moldex3D?
After multiple comparisons amongst the available injection molding simulation software, Shape Corp. chose Moldex3D for plastic flow simulation, validation and optimization in December 2010.
Moldex3D software has now been integrated into our maturation and program management systems. It is no longer a “check-in-the-box†by simply performing the simulation. We are actually using it to help solve potential product issues. We are applying the complete filling, packing, cooling, and warpage analyses with realistic inputs and analysis outputs to the development and manufacturing process of new products at key junctures before launching.
Moldex3D has helped our engineers:
- Determine gating and problem areas prior to mold quoting.
- Validate real mold designs to determine processing parameters.
- Identify issues and correct part or mold design prior to cutting steel.
- Correlate final process in reality with simulation to further improve results on future simulations of new products.
In addition, Moldex3D also serves as a good adviser for providing our quoting group with accurate predictions on cycle time, tonnage and other important process parameters. This helps the quoting group conduct a thorough feasibility review before generating the quote for customers.
However, some may still question the necessity to invest in such CAE simulation software, and one of the most common questions is “How reliable are the simulation results?â€
To answer this, we performed a correlation study on the Moldex3D software to find out the maximum expected accuracy of the simulation compared to the real-world molded parts. We selected 20 common parts with varying sizes, materials, gating schemes, and molding types, applying the real-world process conditions to the simulation. Since the purpose of the correlation study is to assess the reliability of Moldex3D simulation software; therefore, we performed all the pre-processing phase in Moldex3D Designer. We then ran the full analysis (Flow, Pack, Cool and Warp) with production process parameters in Moldex3D eDesign.
Finally, we compared the results of the analysis to the real production processes and ranked the correlation visually and dimensionally. Our results showed a maximum expected accuracy of simulation to reality on filling ranged from 70%, on an aesthetic, complex part designs with multiple sequenced valve gates and highly engineered resin, to more than 91% on a fairly simple structural part with cold gates and simple resin.
Correlation Study Results
Below are two of our correlation studies comparing the simulation filling results with actual shop floor process and molded parts.
The product in the first study is a cowl closeout. The part is positioned near cowls so the tolerance is very crucial to prevent warpage problem. The material used in the study is TPE and the mold type is a two-cavity mold (LH&RH) with cold runner.
            Â
    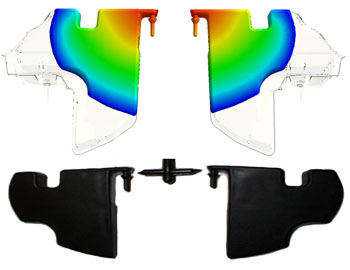
                      Melt Front Time 25%                         Melt Front Time 50%
         Â
     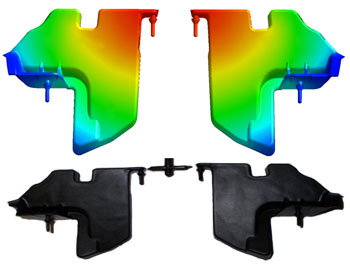
                    Melt Front Time 75%                          Melt Front Time 100%
The second product is an energy absorber (EA), which is widely used as a pedestrian safety solution in the  automotive sector. It is designed to protect the occupants, usually by creating “crumple zones†at each end of the vehicle while preserving a stiff central cage in which the occupants are secured by seat belts and protected by inflatable air bags. This part is going to fit behind the front & rear bumper/ fascia and in front of main chassis. The material used is PP and the mold type is two-cavity mold with hot runner.
In both studies, we took the pictures of the real mold trial and melt front time of 25%, 50%, 75%, 98%, and 100% (as shown below). Then, we compared them with the simulation results and found that both correlation studies demonstrate the simulation analysis results highly correspond with real molded parts.Â
Melt Front Time 25%
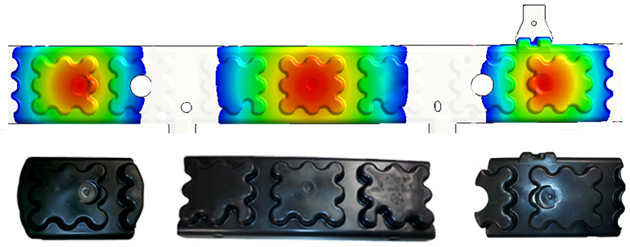
Melt Front Time 50%Â
Melt Front Time 75%Â
Melt Front Time 100%
The Value of Moldex3D
Overall, I am pleased with the outstanding performance of Moldex3D. If you haven’t had a chance to use Moldex3D, you may not appreciate the studies above. However, we were truly impressed by its accuracy, performance and capability. The studies answered many questions and bolstered our confidence in the selection of Moldex3D as our simulation software. In addition, it continues to be a pleasure to work with the Moldex3D support team. They always offer a great level of technical support and training, and strive to help us resolve problems promptly and efficiently.
![]() |
![]() |
TYLER FORBES Global Plastics Technical Manager Shape Corp. |
PRASAD GUNJIKAR Application Development Engineer Shape-Netshape India Team |
Tactical Uniform,Tactical Apparel,Tactical Gear,Tactical Shirts
Foshan Dragon Edge Outdoor Equipment Co., Ltd , https://www.dragon-edge.com