How to prevent the oxidation of general purpose rubber sheathed conductors
General purpose rubber sheathed cable is a type 5 copper conductor as the conductive core. In its production process, copper conductor is often found to be oxidized and discolored. This seriously affects the quality of the product and has become an old technical problem for many cable manufacturers in China. .
Copper is a transition metal and is easily oxidized to black by oxygen in the air under acidic conditions. When the surface of the copper conductor has water film or water droplets, the atmosphere contains a lot of dust, such as smoke, coal, automobile exhaust, chlorides and other acids, alkalis, salt particles, dust, etc. These harmful substances are dissolved in water film or water droplets. In the electrolyte can be formed, thereby accelerating the oxidation of copper conductor discoloration. The light affects the appearance of the product and the quality of the product. In severe cases, the use of the copper conductor is affected, resulting in a waste of production costs. Therefore, the copper conductor must be properly stored, pay attention to oxidation and discoloration.
The principle of copper metal used for cables is that there are physical methods for blocking copper from contact with humid air, cathodic protection with redox to prevent oxidation of copper conductors, chemical methods to form passive films on the surfaces of copper conductors to prevent oxidation, or spraying special liquids on conductor surfaces. protection. Take the production of general rubber cable as an example, the main method of preventing oxidation in each process.
1, copper rod into the factory before transport, testing and storage
2, copper wire drawing process control
3, copper wire stranding (bundle) and insulating rubber, sheath rubber extrusion process
The polyester tape shall be wrapped or wrapped around the conductor before the insulation is extruded, and the material in the rubber insulation shall be placed to corrode the conductor. During the extrusion process, the insulating rubber and sheath rubber should prevent the thread from entering the water, and the oxidation of the thread ends can occur.
Closed Die Forging Parts
According to the classification of forging process, closed die forging and open die forging are commonly used. Closed die forging generally keeps the gap between the upper die and the lower die during the forging process, and the material is formed in the closed die cavity around it. Generally, no flash is generated. A small amount of excess material will form longitudinal flying spurs, and the flying spurs can be removed in subsequent steps. Closed die forging improves the dimensional accuracy and surface quality of the product, reduces flash, and improves the utilization of materials.
SCZY mainly produces hot forging products, both closed die forging and open die forging are produced, which can depend on the requirements of the product. Whether it is closed die forging or open die forging, we will fully consider it during mold development to reduce the occurrence of defective products in the production process. Our own internal mold manufacturing, forging production and subsequent secondary CNC machining can cooperate with each other, which can better ensure product quality and production delivery.
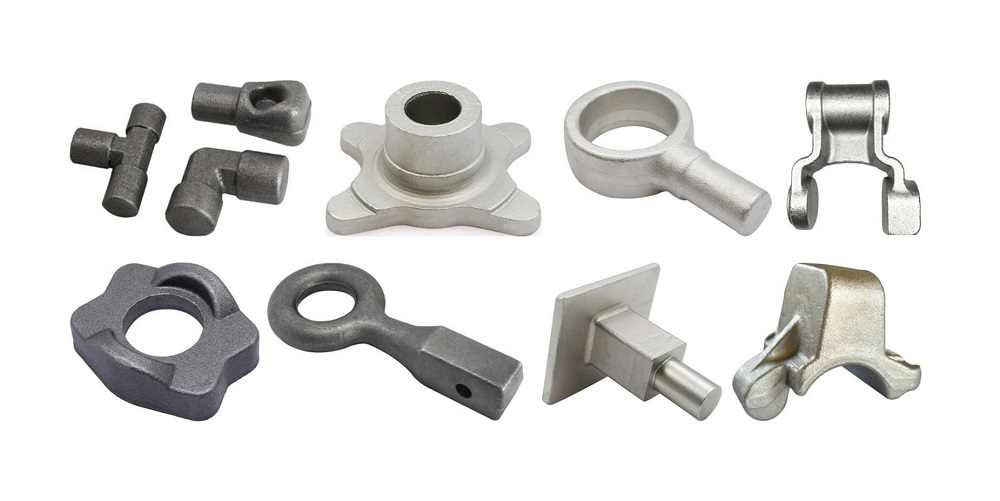
Closed Die Forging Parts,Carbon Steel Closed Die Forging Parts,Closed Die Hot Forging Part,Steel Die Forging Parts,Closed Die forging
Shenzhen SCZY Technology Co.,Ltd , https://www.szcasting.com