Press Brake Terminology: Key Terms Explained
I. Introduction
Mastering professional terminology is of vital importance in the sheet metal industry. Only by understanding the concept of each technical vocabulary can we communicate and accomplish the task better.
Press brake is a common device used in sheet metal fabrication. It can bend the metal sheet into the required shape through pressing down the die. The machine itself has many specific nouns to know.
Our passage aims to introduce the common press brake terminology and its definition, which can help you establish the correct terminology concept cognitive framework and improve your working skills.
Besides, mastering the press brake terminology is not only limited to the name of the machine parts, but it also contains the concept of mastering bending allowance, bending deduction, tonnage calculation, etc., which is indispensable for sheet metal manufacturing arts.
Ensuring a comprehensive understanding of terminology makes it easier to improve the precision of metal forming tasks and effective communication in the working space.
II. Basic Press Brake Concepts
Concept
Press brake is made up of the bed, ram, die, punch, etc., which is designed for bending the metal sheet. Its function is usually determined by accurate communication and a clear understanding of the function and components.
It is widely used in automobiles, machine tools, and electromechanical products, which can effectively accomplish sheet bending fabrication and meet the production needs of different types of models.
Types
Hydraulic press brake: it utilizes the hydraulic-driven system to drive the pressure rod down, which may be challenging to maintain.
Mechanical press brake: it utilizes a mechanical transmission setting to drive the pressure rod. It is simple and cheap, but driving is inconsistent and has immense power.
Electric press brake: it utilizes the AC motor to drive, is fast, and is easy to control, which becomes the future development of oriental
Understanding Press Brake Components
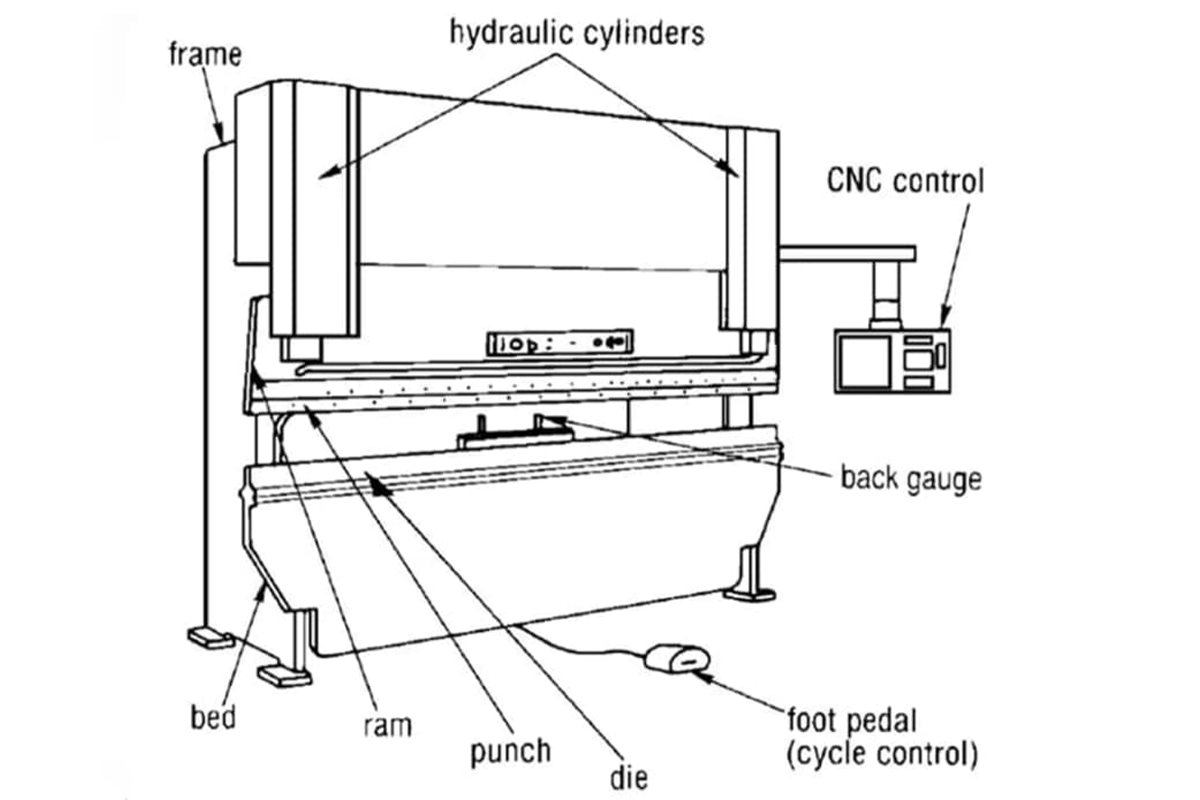
Bed
It is a fixed, flat surface used for the press brake to lie the workpiece. It supports and ensures the bending process is correct and aligned.
Ram
Ram is on the upper part of the press brake, which can be moved downward to exert bending force on the workpiece. It is connected to the punch and directly touches and helps form the metal.
Die
The die is a tooling and part with a specific shape used in the press brake and designed for shaping and forming the material. It is usually installed on the bottom beam.
Punch
The punch is also the tool and part with specific shapes used in the bending process for making materials to form. It is usually installed on the upper beam.
Back gauge
The back gauge is the mechanism and CNC controller installed on the rear of the press brake bending area. It is composed of the fingers and stops and is designed to position the bending material precisely, which can ensure a consistent and accurate bending operation.
Back gauge origin
The back gauge origin is the reference point measured on the back gauge system. It ensures the starting location of the back gauge during the bending operation.
CNC system
CNC is the abbreviation of the computer numerical control. It refers to a control system utilizing computer programs to control the machine movement automatically, which includes back gauge, ram, and other axes.
Upper beam
The upper beam is a movable beam or punch of the press brake, which can exert pressure on the material to perform bending. It fixes the punch and exerts the pressure via vertical movement.
Lower beam
The lower beam plays a vital role in press brake fixing, which can offer support for die or bottom tools. When the upper beam or punch moves vertically to exert bending operations, it will keep stable.
X-axis
The X-axis refers to a horizontal axis that can control the back gauge moving along the press brake length. The operator controls the back-and-forth movement of the back gauge, thus ensuring the flange length.
Y-axis
The y-axis is a vertical axis that can control the movement of the press brake punch or upper beam. The ram's vertical movement is called the Y axis. If the press brake is equipped with two independent cylinders, the CNC press brake can directly control each side of the cylinder. The left side of the ram is Y1, and the right side of the ram is Y2.
Z axis
The z-axis refers to the horizontal axis that moves or stops along the left and right locations. The Z-axis is used to measure the location and movement of the back gauge.
R axis
The R axis is used to control the back gauge finger's vertical movement or stop. It can bend complex shapes or achieve multiple bends. The back gauge vertical movement is the R axis, which can be controlled on some CNC press brakes. R1 and R2 refer to the up and down movement of the left and right back gauges.
Sheet support arms
These sheet support arms are extended parts installed on the front of the machine, which are used to support the workpiece during bending. Sometimes, they can measure the workpiece.
III. Advanced Terminology and Techniques
Bend allowance
Bend allowance refers to material deformation or elongation required by forming a specific bending angle. It is calculated according to material thickness, bending radium material characteristics, etc.
Bend deduction
Bend deduction refers to the difference between the sum of the layout dimensions and the total length of the curved part. It shows the length of the consumed material during the bending process.
Bottom dead center
The bottom dead center refers to the lowest point the punch or upper beam arrived at during the downward stroke.
Braking capacity
Braking capacity refers to the biggest force or tonnage exerted by bending specific material inside the machine's operation restriction.
Clutch
A clutch is a mechanical device used in the press brake. It can be used to connect or interrupt the power transmission from the motor to the punch. It controls the movement and stop of the ram during the bending process.
Bottom bending
Bottom bending is a technique in which the upper beam exerts pressure to bend the material into the complete shape of the die. Compared with air bending, the bottom bending keeps the punch and die closer. Thus, more tools will be in contact with metals, and bending can better match the shape of the punch and die. Bottom bending needs more tonnage than air bending.
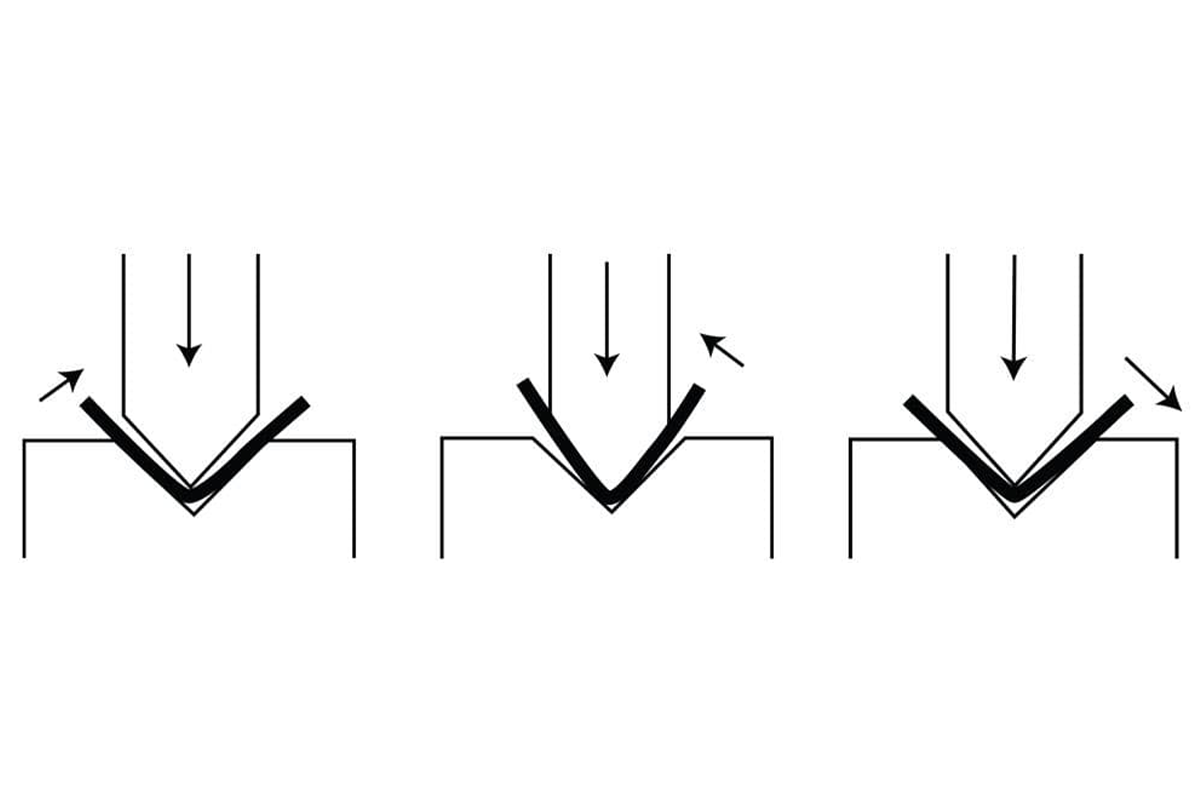
Air bending
Air bending is a bending technique that only uses 3 contact lines to bend the material. The material will not arrive at the bottom thus there will be a more flexible and widespread bending angle.
Compared with other bending methods, air bending gets less in touch with the metal. The bending angle is determined by the depth the punch descends into the die instead of the actual shape of the workpiece itself.
Coining
Coining is a precise bending technology. It presses the material into the die to achieve high precision and correct bending angle. Coining originates from the metal manufacturing process for making coins, which uses extremely high tonnage to compress metal, and makes the metal the same as the die’s angle.
Spring back
Springback is a trend in that material returns to its original shape after being bent. When the material is bent and released, it will show some spring back, resulting in the bending part being slightly straightened or deformed.
Daylight
Daylight refers to the distance between the upper beam and bottom beam of the press brake when it completely opens without material or tools. It determines the maximum height of material that machines and tools can accommodate. That is the biggest material size that can be put in the press brake. The normal daylight ranges from 12-24 inches.
Deflection compensation
Adjust the press brake crowning system to compensate for deflection, ensuring accurate bending results.
Deflection
Press brake components (such as the upper beam and bottom beam) will be bent and deflected because of exerting forces during the bending process. Deflection will affect the accuracy and repeatability of the bending operation.
Elasticity
Elasticity is a characteristic that can cause the material to be retrieved from its original shape when influenced by the outer force. Press brake uses material elasticity to achieve the required bending angle.
Elongation
Elongation refers to the amount of material deformation and stretching during the bending process. It is shown by percent and determined by material characteristics and bending parameters.
Flange
Flange refers to the flat or extended part that material remains unbent during the bending operation. It offers stability and can be regarded as a connecting point of the component or structure.
Gibb adjustment
Gibb adjustment is a process for adjusting the guiding device. The guiding device is a mechanical components that control the press brake punch and frame gap and stability movement.
Inside bend radius
The inside bend radius refers to the radius of curvature of the bending material's inner surface. It is measured by the center line to the innermost point of the bend.
Inside setback
Inside setback refers to the distance between the material edge and the bending line of the bending inner side. It can ensure the correct positioning of the material and achieve accurate bending.
K factor
The k factor is the modulus used in press brake bending calculation, which is used to ensure neutral axis position and bend allowance. It takes the material characteristics into consideration like thickness, stretch rate, and stretch tensity.
Mechanical stop
A mechanical stop is a physical stop or limiter on the press brake back gauge system, which is used in controlling the material position and ensuring accurate and consistent bending.
Minimum inside radius
The minimum inside radius is the minimum radius that can be achieved during the bending operation process. This will not result in acceptable material damage or deformation.
Neutral axis
The neutral axis is the center axis or line, which keeps constant during bending. When it is stretched and compressed, it almost will not deform.
Outside setback
Outside setback refers to the distance between the edge of the material and the bend line outside the bend. It ensures correct material position to achieve precise bending.
Pinch point
The pinch point refers to the area between the upper and bottom beams, where the material will be squeezed during the bending. Keeping the finger and hand away from pinch points is of pivotal importance.
Stroke length
Stroke length refers to the moving distance of the press brake punch or upper beam in vertical movement. It determines the maximum bending depth that can be achieved.
Swing up finger
Back gauge fingers or stops can be swung upward and retracted, allowing larger or wider components that bend beyond the normal back gauge range.
Tandem
A tandem is a device that two press brakes that can be used together to operate bending on a long or wide sheet. It can improve capacity and flexibility.
Tensile strength
Tensile strength refers to the biggest stretch force that the material can be bent before broken or invalid. This is the factor to be considered when choosing the bending material.
Throat
Throat refers to the maximum depth distance ranging from the center line of the bottom beam to the frame. It determines the biggest depth of the material that can be bent across its entire width.
Top dead center
The top dead center is the highest point arrived by the punch or upper beam of the press brake during the upper stroke.
IV. Conclusion
Our passage mainly talks about the basic concept of the press brake and relevant terminologies, which may assist you in mastering industry knowledge.
If you want to know more about the press brake knowledge, welcome to browse our official website for machine learning or purchasing!
Distributor Plate,Vsi Crusher Wear Part,Distributor Tip For Mining,Carbide Rotor Distributor
Zigong Tianyi Industry Co., Ltd , https://www.tyhpgrcarbidestud.com