Three major detectors help develop the aerospace industry
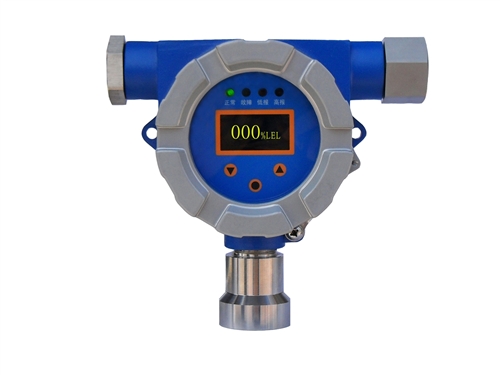
Gas detector for space shuttle
On the first spacewalk mission, an IC Cisco CSA-CP (TX418) gas detector was installed on the left bulkhead. They took the NASA Shuttle Endeavour for their final mission. Before going out of the tank, they must wear these oxygen hoods a few hours in advance to draw pure oxygen to remove nitrogen from the body to help avoid any “dive vertigo†if they get out of the cabin too quickly and experience low blood pressure. Not available, there will be a similar feeling of diving. RonGaran and MarkKelly took photos with them at the air lock of the space station. The space suits on the left and right were worn by Drew and Greg before they got out of the cabin.
American Industrial Scientific Corporation is a world-renowned company specializing in the design, manufacture and sale of industrial-grade portable and fixed toxic and hazardous gas detectors. Industrial Scientific has become synonymous with robust and reliable gas monitoring instruments worldwide.
The Industrial Scientific MX6 multi-parameter gas detector has become a domestic R&D and production enterprise for rescue cabins and refuge chambers due to its excellent quality, accurate measurement data, easy use of pump-type integrated machine, and superior waterproof and dust-proof level to domestic products. Gas detector of choice. At present, dozens of companies in the rescue and evacuation shelters have already chosen this equipment and have received unanimous praise from the competent authorities and users.
Laser Ultrasonic Visual Detector Breaking Through Aerospace Nondestructive Testing
The laser ultrasonic visual detector technology was officially approved by Xi'an Aviation Base. The localization of this technology has filled the gaps in the industry, greatly narrowing the gap between the development and production of non-destructive testing instruments and the developed countries in the world, and is a major breakthrough in the field of NDT in China.
Non-destructive testing has always played a pivotal role in the quality management of various manufacturing industries. Among them, ultrasonic inspection has been widely used due to its safety, economy, and convenience, but it cannot be used to efficiently and intuitively detect any complex shape and internal defects of non-metallic objects. With the wide application of new materials such as carbon fiber composites and ceramic matrix composites, the aviation industry has also achieved unprecedented development. However, the non-destructive testing of these new materials has so far lacked effective means.
According to the Instrument and Meter World Network, the laser ultrasonic visual instrument developed by Xi'an Jinbo Detection Instrument Co., Ltd. has successfully broken through this world scientific research problem in the field of non-destructive testing. The appearance of the detector can detect the internal and external parts of any shape objects and most materials, from electronic components to large parts of the aircraft, and can perform non-destructive testing, and can work in harsh environments such as high temperature and toxic. The use of laser ultrasonic visual inspection instruments to regularly inspect high-speed vehicle parts such as aircraft wings and train axles, as well as power generation equipment and pressure vessels, etc., can extend its safe lifespan to the maximum extent and avoid major accidents.
If the traditional ultrasonic non-destructive testing technology is likened to "radio" technology, the laser ultrasonic visual non-destructive testing technology belongs to "television" technology. The laser ultrasonic visual inspection instrument is composed of a detection unit and a laser unit, and can simply visualize the propagation process of the ultrasonic wave, and inspect the damage of the inside or the surface of the measured object according to the waveform change, and can be observed clearly and in real time through the computer screen. Because the laser ultrasonic visual inspection instrument technology realizes the visual inspection of non-destructive testing, it becomes very easy to identify defects and damages existing inside the object, and it can prevent the missed detection and misjudgment that often occur in non-destructive testing.
Radio fault tester was born
Recently, a tester capable of quickly detecting the failure of aircraft VHF communication system was successfully developed at Southern Airlines Henan Branch. According to reports, this research achievement has filled China's technological gap in this area.
The aircraft VHF radio is an important device for communication between the crew and the ground. With the increase of aircraft use time, the failure of the radio antenna circuit has increased significantly. Since the VHF radio transceivers of most aircraft currently do not have the antenna self-checking function, it is difficult for the maintenance personnel to quickly determine whether it is an antenna failure or a transceiver failure during the inspection in the field, which is time-consuming and labor-consuming and reduces the safety of the aircraft. Performance and daily utilization.
The “handheld digital airborne VHF radio fault tester†developed by electronic engineers Yin Zhihang and Zheng Xiang is mainly composed of integrated circuits. The volume is only the size of a box and can be digitally within 10 meters of the aircraft. Accurately shows the actual launch power amplitude of each VHF radio station of the aircraft to help the maintenance personnel to quickly and accurately determine the types of failures, to effectively prevent accidental exchange of high-priced aviation materials, and to improve the civilian and military aircraft communication systems. Faulty maintenance quality. At present, this type of tester has been put into use at the China Southern Airlines Henan Aircraft Maintenance Factory.
Rail Gap Adjuster And Regulator
Hydraulic rail gap adjuster is to solve the problem of railway rail joint clearance (that is, rail gap) due to climate change and driving factors, such as its size change constantly. To make the rail gap back to the required size, must be string dynamic rail.
Hydraulic Rail Gap Adjuster Railroad High Efficiency Rail Gap Regulator Equipment has push and pull small rail joint two functions, pushing rail, rail pulling all can, easy operation, high efficiency, with its anti "card dead" function, the use of safe.
Rail Gap Adjuster,Rail Gap Regulator,Hydraulic Rail Device,Rail Gap Adjuster And Regulator
Shenyang Lubang Railway Maintenance Machinery Co.,Ltd. , https://www.srmfrailwayequip.com