Vulcanizing Press for Rubber Synthetic Rubber Production Line 315 Ton
Vulcanization & Rubber molding
Forming the future with ZHENGXI
System solutions for Rubber
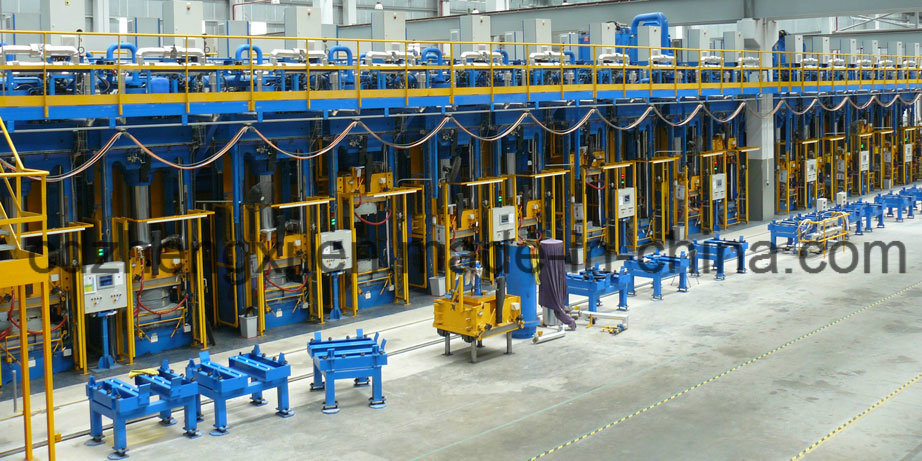
Rubber Industries
Production of raw NR might be classified as an agricultural industry because latex, the starting ingredient, is grown on plantations in tropical climates. By contrast, synthetic rubbers are produced by the petrochemical industry .Finally, processing into tires and other products occurs at processor (fabricator) plants, commonly known as the rubber industry .The company names include Goodyear, B. F. Goodrich, and Michelin, all reflecting the importance of the tire.
Rubber Processing and Shaping
Production of rubber goods consists of two basic steps:
- 1.Production of the rubber itself
- 2.Natural rubber is an agricultural crop
- 3.Synthetic rubbers are made from petroleum
- 4.Processing into finished goods, consisting of:
- Â 5.Compounding
- 6. Mixing
- 7. Shaping
- 8. Vulcanizing
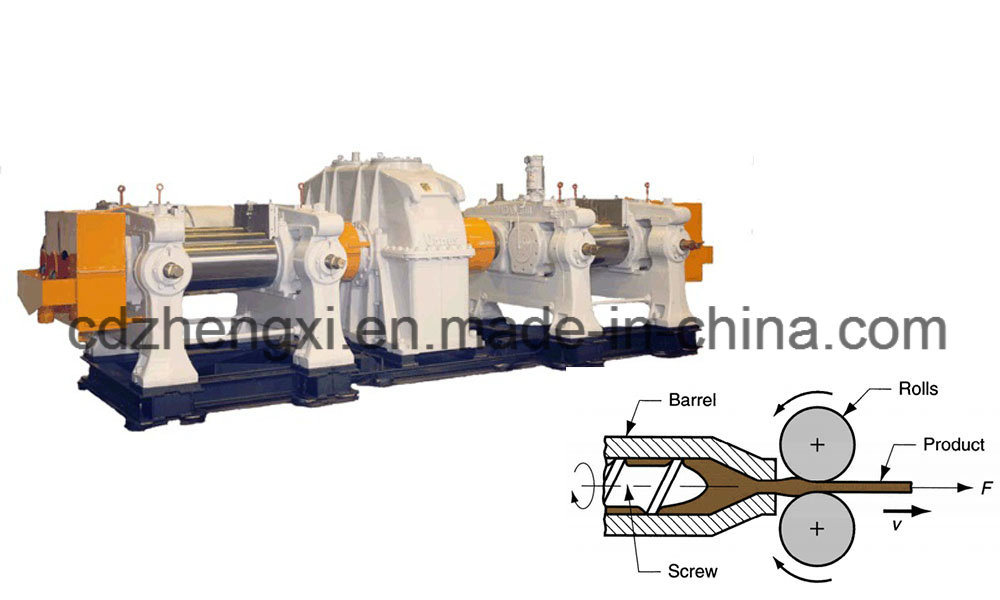
When it comes to producing rubber products, multiple manufacturing processes exist. Each manufacturing process has particular benefits that make it the ideal choice for manufacturing certain types of products. Knowing the manufacturing processes can help you understand cost implications and tradeoffs. Some of the most common rubber manufacturing processes are extrusion, latex dipping, molding, and calendering.
The additives must be thoroughly mixed with the base rubber to achieve uniform dispersion of ingredients
1.Uncured rubbers have high viscosity so mechanical working of the rubber can increase its temperature up to 150°C (300°F)
2.If vulcanizing agents were present from the start of mixing, premature vulcanization would result - the "rubber processor's nightmare"
The most common manufacturing process is called calendaring, which works by forcing softened material into the center of counter-rotating rollers. Rollers compact the material and the overall thickness of the product is determined by the gap distance between cylinders, which can be adjusted for varying product thicknesses. Once the material passes through cooling rollers, it must be vulcanized. This process works best to produce sheets or films of rubber. Some benefits of calendering include control over product thickness and the ability to produce parts thinner and wider than with the extrusion. However, calendering has high operating costs compared to other processes.
Vulcanization & Â molding
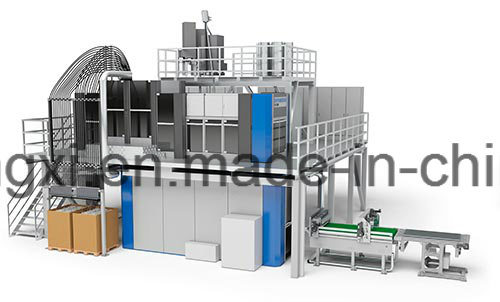
Vulcanization or vulcanisation is a chemical process for converting natural rubber or related polymers into more durable materials by heating them with sulfur or other equivalent curatives or accelerators. These additives modify the polymer by forming cross-links (bridges) between individual polymer chains.Vulcanized materials are less sticky and have superior mechanical properties. The term vulcanized fiber refers to cellulose that has been treated in a zinc chloride solution to cross-link the cellulose fibers.
Although curing of rubber has been carried out since prehistoric times, the modern process of vulcanization was not developed until the 19th century, mainly by Charles Goodyear. Today, a vast array of products are made with vulcanized rubber, including tires, shoe soles, hoses, and conveyor belts.
Â
The term "vulcanization" is named after Vulcan, the Roman god of fire. Hard vulcanized rubber is sometimes sold under the brand name Ebonite or the genericized former brand term "vulcanite", and is used in making articles such as clarinet and saxophone mouth pieces, bowling balls, and ice hockey pucks.
Each manufacturing process is ideal for producing certain types of rubber products. Understanding the processes available can make planning for manufacturing a lot easier because each process has its own cost and time limitations.
Â
ZHENGXI has developed and implemented hundreds of hydraulic presses for rubber, plastics & composites applications all over the world. Apart from multi-platen press solutions, we serve the rubber industry with compression molding press dedicated to tire production.
Application
1. Aerospace
Re-useable silicone vacuum bags, pressure bladders, caul sheets, extrusions, compaction bags, molded parts, silicone sheet fluoroelastomer, tool sealant, infusion products.
2.Gasket Supplies
Silicone sheet, fluoroelastomer sheet, molded pads, sponge sheet, fabric reinforced sheet.
3. Automotive
Gasket material, extrusions, fluoroelastomer sponge sheet.
4. Composite Manufacturing
Re-useable vacuum bagging material, seals, caul sheets, tool sealant, vacuum infusion products.
5. Cabinet Manufacturing
ParameterÂ
Model  | unit | Yz33-200T | Yz33-315T | Yz33-500T | Yz33-650T | Yz33-800T | Yz33-1000T | Yz33-1250T | |
Nominal Force | KN | 2000 | 3150 | 5000 | 6500 | 8000 | 10000 | 12500 | |
Max working pressure of liquid | MPA | 25 | 25 | 25 | 25 | 25 | 25 | 25 | |
Plate press | KN | 630 | 1000 | 2000 | 2500 | 3150 | 4000 | 5000 | |
Max. open height | mm | 1200 | 1500 | 1600 | 1700 | 2000 | 2300 | 2500 | |
Stroke | mm | 700 | 800 | 900 | 1000 | 1100 | 1200 | 1500 | |
Plate stroke | mm | 250 | 300 | 350 | 350 | 400 | 400 | 500 | |
Slide speed | Down | mm/s | 80 | 120 | 120 | 200 | 300 | 270 | 300 |
Pressing | mm/s | 10~20 | 10~25 | 14~35 | 10~35 | 10~35 | 10~35 | 15-30 | |
Return | mm/s | 80 | 130 | 115 | 150 | 150 | 270 | 200 | |
Table size | Left-right | mm | 800 | 1600 | 1800 | 2400 | 3000 | 3600 | 4600 |
Front-back | mm | 800 | 1200 | 1600 | 1800 | 2000 | 2400 | 2400 | |
Plate size | Left-right | mm | 600 | 1200 | 1400 | 1800 | 2200 | 2600 | 3600 |
Front-back | mm | 550 | 800 | 1100 | 1200 | 1300 | 1500 | 1500 | |
Motor power | KW | 22 | 44 | 60 | 74 | 90 | 110 | 190 | |
Type | Â | Four-column | Four-column | Four-column | Four-column | Frame | Frame | Frame |
Factory details
Certificate
After-sale service
1.Personnel training
Free training for about one week.
2. After-sale service
One year warranty.During warranty period,free maintenance service can be provided.(except man-made faults or damages arising from irresistible natural factors)
3.Installation
Customers need to pay the commission to our proffessional engineer, and travel expense is on foreign customer.(Including round ticket and accommodation cost)
Transform Your Ride with LDC VINYL!
Welcome to LDC VINYL, your ultimate destination for turning ordinary vehicles into extraordinary works of art! If you're looking to make a bold statement on the road, capture attention wherever you go, or elevate your brand visibility, you've come to the right place.
At LDC VINYL, we specialize in crafting custom vehicle wraps that transcend the boundaries of imagination. Our team of skilled designers and technicians are dedicated to transforming your car, truck, van, or even your entire fleet into stunning colors that reflect your personality, brand identity, and unique style.
Imagine cruising down the streets with an eye-catching masterpiece that not only reflects your individuality but also showcases your business to a wider audience. Whether you're an entrepreneur looking to advertise your services on the go or an individual seeking to add a personal touch to your vehicle, our cutting-edge vehicle wraps offer a creative and cost-effective solution.
Why Choose LDC VINYL for Your Vehicle Wraps?
LDC VINYL leverages top-tier PVC film as its foundational material, synergizing precision coating and bonding techniques. Crafted for both automotive exteriors and interiors, this product boasts vibrant and dazzling colors coupled with exceptional weather resistance. By incorporating an ultra-low initial adhesive for easy removal and the fourth-generation diamond-shaped air channel technology, it significantly enhances installation efficiency. Fulfilling the comprehensive or selective vehicular adornment needs of consumers, LDC VINYL stands as a prime choice for automotive coating.
Brand Advantage
(1) Integrated Full Chain Production: Integrating color development, precise coating, and adhesive lamination into a seamless process, each production phase interlocks, ensuring excellent product quality.
(2) Exquisite Film Surface: Carefully selected from top-tier polyvinyl chloride base films, sourced entirely from Nan Ya Plastics and Renolit. Combined with mature coating and lamination techniques, the resulting film boasts a delicate, smooth texture, thin and pliable, easily stretchable without any opacity.
(3) Vibrant and Rich Colors: Employing a base film of the same color family, alongside precise coating techniques and exceptional color layers, each shimmering particle is uniformly distributed. This meticulous arrangement achieves a naturally gentle hue, vibrant and rich in color, faithfully recreating the distinct texture of automotive paint.
(4) Superior Weather Resistance: Utilizing automotive-grade metallic pigments and dyes, in conjunction with high-molecular polyvinyl chloride base film, the film's outdoor durability is enhanced. This ensures color remains vivid and stable over time. All products undergo UV accelerated aging and 2000-hour xenon lamp testing.
(5) Low Initial Adhesive, Removable Backing: Employing high-quality ultra-low initial tack pressure-sensitive adhesive, paired with a high-performance PET release liner. Through mature adhesive production processes, products achieve low adhesion for easy application, remaining weather-resistant without adhesive residue.
(6) Stringent Color Deviation Control: All products utilize high-quality raw materials and employ mature production processes to achieve color stability. Throughout the production process, each step is precisely color-matched against standard samples, ensuring batch-to-batch color consistency.
(7) Three-Tier Quality Control: The company has established laboratories and testing centers, implementing a three-tier quality control system. From raw materials to finished products, each undergoes rigorous company test
Car Wrap,Car Vinyl Film,Vinyl Wrap,Vehicle Wrap
Guangdong HANTAI Decoration Material CO., LTD , https://www.ldccarwrapfilm.com